Six Sigma Yellow Belt
- Understand the lean principles in the organization
- Understand how Quality Function Deployment fits into the DFSS process
- Analyze the difference between DFMEA and PFMEA
- Learn to identify process owners, internal and external customers, and other stakeholders in a project
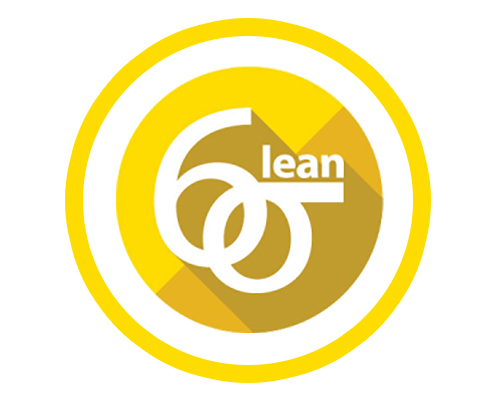
Overview
Our Six Sigma Yellow belt course aims to provide delegates with an understanding of the fundamentals of Six Sigma so that they can contribute to Green Belt projects and know how to apply basis tools within a DMAIC or Problem Solving process on a routine basis. We provide Online Six Sigma Yellow Belt Training and Certification. Yellow Belt is the entry level certification of Six Sigma. Six Sigma is a step-by-step process of interventions and statistical tools that allows companies to interpret which business processes need attention, identify root causes of problems, and sustain gain in improvements.
Course outline
Lean Six Sigma Introduction
- SESSION 1-Introduction
- Higher Standards for Higher Performance
- Lean Six Sigma Defined
- What’s In a Name?
- The 5 Lean Principles
- Success Stories
- Input Determines Output
- The 99.9% Problem
- The Sigma Level
- DNA of a Champion
- Lean Six Sigma Framework
- DMAIC – The Lean Six Sigma Improvement Process
- Lean and DMAIC
- Organizing for Success
- Working Relationships
- Session1 Skill Check
Tools To Define
- SESSION 2 – Introduction
- Project Charter Toolset
- Focus on The Customer
- Capturing The Voice Of The Customer
- Where to Go For Customer Requirements
- Affinity Diagram Toolset
- CTQC Tree Diagram Toolset
- Voice Of The Customer As Specifications
- Process Thinking
- The Source of Value
- Value Stream Leverage
- Process Mapping – Overview
- Process Mapping (SIPOC) Toolset
- Flow Charts
- Value-Added Flow Charts
- Spaghetti Charts
- Value Stream Mapping Toolset
- Session 2 Skill Check
Tools To Measure
- SESSION 3 – Introduction
- Measurement & Metrics
- Measurement As A Process
- Baseline Performance
- Calculating the Sigma Level – Toolset
- Trend Chart Toolset
- Histogram Toolset
- Quantifying Process Variability
- SPC – Introduction and Background
- X and Moving Range Charts – Toolset
- Pareto Chart Toolset
- Session 3 Skill Check
Tools To Analyze
- SESSION 4 – Introduction
- Cause & Effect Diagram Toolset
- 5-Why, 1-How
- Scatter Plot Toolset
- Correlation and Regression Analysis
- Session 4 Skill Check
Tools To Improve
- SESSION 5 – Introduction
- Brainstorming
- Benchmarking
- FMEA Toolset
- Continuous Flow Toolset
- Quick Changeover Toolset
- Pull Scheduling
- Error-proofing
- Prioritizing and Selecting a Solution
- The A3 One-Page Report
- Piloting a Solution
- Session 5 Skill Check
Tools To Control
- SESSION 6 – Introduction
- Control Charts Revisited
- 5-S Approach
- Visual Control
- Control Plan
- TPM Objectives & Benefits
- Standardized Work – Documenting Process Changes
- Session 6 Skill Check
- Course Completion
- The Lean Six Sigma Journey
Key Features

- 8 hours Instructor led Online Training
- Soft copy of Study materials
- Course Completion Certificate
- 8 PDU/1 CEU Certificate
- 100% Money Back Guarantee
- Flexibility to choose classes
- Certifies trainer
- 2 Simulation Test
- Training by Certified World class trainer
- Industry wise – Real life practical examples
- Post training support
- 10% discount on any other Course
Course Objectives
- Understand the value of Six Sigma
- Understand organizational drivers and metrics
- Understand Organisational goals and six sigma projects
- Understand the lean principles in the organization
- Understand how Quality Function Deployment fits into the DFSS process
- Analyze the difference between DFMEA and PFMEA
- Understand the road map for DFSS (Design for Six Sigma)
- Analyze the process elements (Recognize how processes cross various functional areas and the challenges that result for process improvement efforts)
- Learn to identify process owners, internal and external customers, and other stakeholders in a project
- Learn to identify how projects impacts the customers
- To identify various methods for collecting the feedback of the customers
- Learn to use graphical, statistical and qualitative tools
- Learn to convert customer feedbacks into project goals and objectives
Who should attend
- Those who wish to become part of companywide Six Sigma practices and/or Improvement Projects
- Working Executives who want to become Six Sigma Experts. (e.g. Quality Assurance Engineers, Project Managers, Team leaders, Software Professionals, Practitioners, Software Quality Assurance team members and Senior Management)
- Those who want to get certified as Green Belt in Six Sigma
- Future managers
- Any other professional members who are doing research, innovations or consulting in process improvement practices
- Management and Engineering Students are desirous to be more resourceful and employable
Pre-requisites
The Lean Six Sigma Yellow Belt training and certification exam has no experience or education requirements.